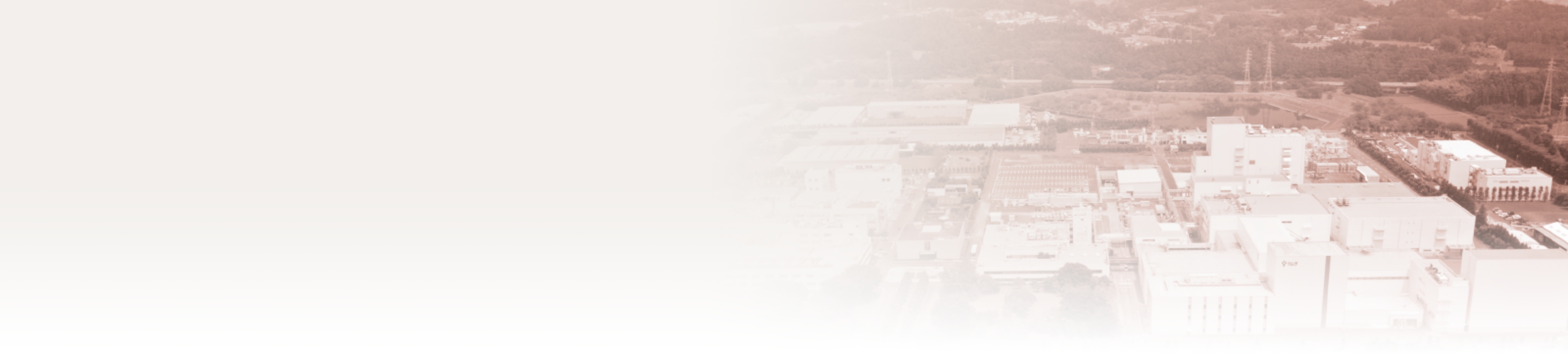
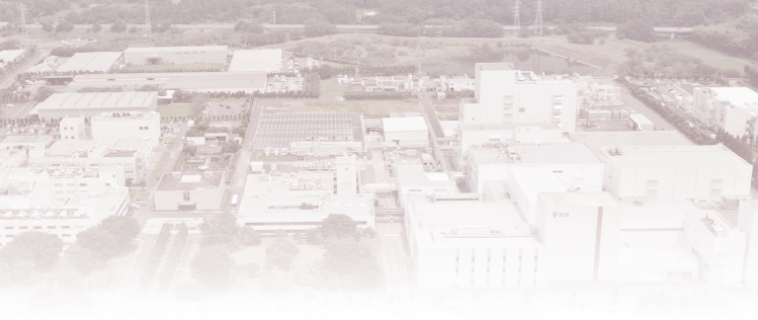
The Kampo Value Chain
We aim to become a value-creating company that continues to grow with society, creating value for our community through the Kampo value chain, while meeting the United Nations Sustainable Development Goals (SDGs).
STEP 1
Cultivation and procurement
-
1
-
Cultivation and procurement of crude drugs
When purchasing crude products from the market, it’s impossible to know the type and amounts of pesticides used, and products from multiple fields and different production areas are often mixed together. Additionally, crude products are required to meet a designated quality level in order to be used as raw materials for pharmaceuticals. Strongly believing that "Kampo begins in the fields," we procure most of the crude products to be used as raw materials from production companies (farmers) through cultivation contracts so as to properly manage cultivation methods and agricultural chemicals used. We also harvest wild products of the same quality level.
-
2
-
Preparation and storage
Locally procured crude products are identified by an inventory management system through barcode ID cards that ensure their traceability. Those that meet our standards are processed by removing unnecessary parts, drying, steaming, and by carefully checking for foreign substances and impurities.
-
3
-
Quality testing, sorting and storage
We then carry out quality testing and sorting by checking for residual pesticides, microorganisms, heavy metals and subsequently store the crude products in warehouses at low temperature (59 °F) and low humidity (60% or less) conditions to prevent a drop in quality.
STEP 2
Manufacturing
-
4
-
Cutting
After crude products are stored in their original form and transported to our factories, they are checked for authenticity, batch number and quantity, and then cut into particle size by using different cutting machines tailored to each type of plant in order to make the most of them. The amount of ingredients to be cut is based on the unit amount of herbal formulations to be produced. Ingredients are used immediately after cutting to prevent a drop in quality.
-
5
-
Weighing and blending
Once cut, crude products are weighed according to the predetermined composition of each preparation. After that, they are placed into a large stainless steel mixing container where their mass is checked once again and then advanced to the extraction process.
-
6
-
Extraction, separation and condensation
Extraction is conducted according to traditional Kampo methods with our own proprietary equipment. At Tsumura, we use our own extraction vessels and purified water to perform hot water extraction (decoction) of crude products. This is done to equalize the quality and quantity of extract powder. Condensing liquid extracts at low temperature and under vacuum with a continuous film evaporator reduces condensation times and prevents loss of bioactive components.
-
7
-
Extraction, separation and condensation
The condensed liquid is sent to a large spray dryer for drying. The liquid is mist-sprayed from the top of a large spray-drying device developed by Tsumura, so that it dries and cools down instantly at the same without being affected by heat, thus becoming a powdered extract hat maintains the original quality.
-
8
-
Granulation and packaging
The powdered extract is mixed with excipients (inactive ingredients) and compressed into tablets by a tableting machine. After being crushed and sized, the resulting granulated extract is classified as heterogeneous, small, or product grade, with only product grade granules qualifying for the final product. Such dry granulation method, ensures that there is no change in component properties during granulation. After passing strict quality checks, extract granules are packed in sheets containing a daily dose of them, bundled in 7 sheets (one week’s supply), packed in boxes and shipped.
-
9
-
Shipping, storage and delivery
The final products are shipped from our Shizuoka and Ibaraki plants and stored at distribution centers in Japan.